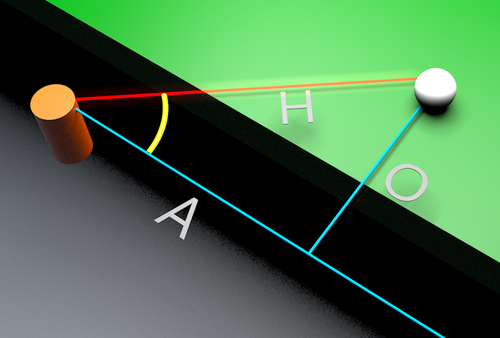
Lidar Table Tennis
2018-09-29
Recently I built an augmented table tennis game which required detection of each bounce of the ball on the table. The simplest idea I could think of was to use a scanning laser rangefinder (AKA LiDAR) scanning a 2D plane just above the surface of the table. I knew there were already several software products to interpret the data from these devices and convert it into TUIO. TUIO is built over OSC, which is a...
Read More